ダイカスト鋳造コンピュータシミュレーションの進歩
Progress in Computer Simulation of Die Casting
2008 日本ダイカスト会議論文集に掲載
1.緒言
最近ダイカスト鋳造においてコンピュータシミュレーションを利用することが多くなってきた.鋳物の品質を向上し,生産性を向上させ,納期を短縮させるのに役立つようになったためである.特に,湯流れ,凝固,欠陥予測の分野におけるシミュレーション技術は最近飛躍的に進歩してきている.ここでは,市販の鋳造シミュレーションソフトCAPCASTを例にとってダイカスト鋳造コンピュータシミュレーションの進歩について紹介する1)〜4).
2.メッシュ作成方法
鋳造シミュレーションの手法には大きく分けて直交差分法と有限要素法の2種類がある.それぞれの特徴を表1に示す.最も大きな特徴は形状モデルのメッシュの差である.立方体または直方体の要素のみで計算するのが直交差分法であり,任意の6面体,5面体等の要素を用いるのが有限要素法である.直交差分法ではメッシュ作成は容易であるが,サイコロを積み上げたような形状表現になり形状精度が悪い.最近では,直交差分法のこの欠点を補うために,規則−不規則混合要素5),CIP法による改善6),ポロシティメディア法7)が開発されてきた.表1中にはポロシティメディア法についての比較も整理した.
表1 メッシュ形状によるシミュレーション手法の比較 |
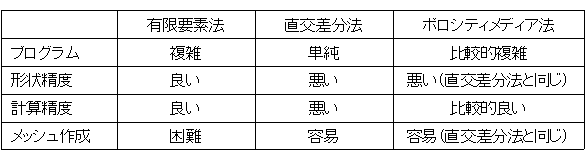 |
有限要素法では,任意に形状を変形できる要素を用いるために,形状モデルの精度が良いが,反面メッシュ作成が困難なのが欠点である.これを解決するために自動メッシュ作成機能が進歩してきた.
3次元CADの普及に伴い,鋳物の凝固シミュレーションにおいてもCADデータが利用できるようになってきた.CADのソフトウェアの種類は多くあるが,STL等の共通フォーマットでサーフェスの形状データが出力できる.これを用いて凝固シミュレーション用の形状モデルの作成が容易に行われるようになってきた.
STLフォーマットのCADデータの一例を図1に示す.鋳物,鋳型(片側のみ表示),入れ子の各部分の表面を3角パッチで囲ったものである.これを有限要素法の自動メッシュ作成プログラムの一つであるCAPCASTで作成した形状モデルを図2に示す.この例では,各部分の表面以外の部分は直方体で分割し,表面付近は任意形状の要素で分割している.市販されている多くの有限要素法の自動メッシュ作成プログラムは4面体(テトラ要素)のみでメッシュ切りを行っている.湯流れ,凝固,変形シミュレーションにおいて計算精度を向上させるためには4面体のみのメッシュよりもほとんどが直方体で表面のみが変形要素で作成したメッシュのほうが有利である.
また,図2において,鋳型は上型,下型,入れ子が別々の部分としてメッシュ分割されている.個々の部分同士は所定の熱伝達率で熱移動がなされる.鋳型が開いて鋳物が取り出された後は,鋳物キャビティとの界面や見切り面で大気に解放された界面では大気への放熱がなされる.スプレーやエアーを吹き付ける場合には大きな熱伝達率で放熱が行われる.
各種のメッシュモデル図を図3に示す.(a)は自動メッシュ切りで作成した直交メッシュで,鋳物表面に直角の凹凸がある.(b)は4面体と5面体要素を鋳物表面に使用して(a)の要素を改良したものである.混合メッシュと呼ばれている.(c)は(b)をさらに改良して形状精度を良くしたものである.(d)は手動で作成したメッシュである.(c)の自動で作成したメメッシュは手動で作成したものと形状精度が劣らないことがわかる.
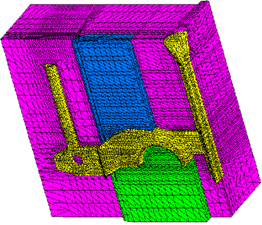 |
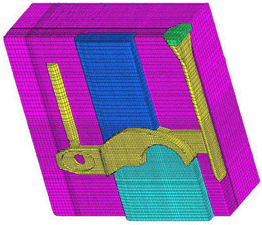 |
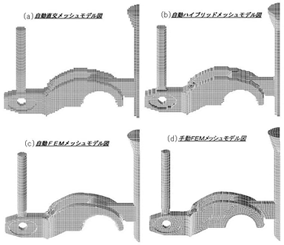 |
図1 STLフォーマットのCADデータ |
図2 自動FEMメッシュモデル |
図3 各種のメッシュモデル |
Page TOP
3. 流動停止シミュレーション
駒崎,蓮野ら8)9)はダイカストにおける湯流れ性を評価するために,図4に示すような薄肉弓字状テストピースを使用した.流動停止の解析結果を図4に示す.
ゲート速度の増大とともに流動長が長くなることが分かる.流動長とゲート速度の関係を図5に示す.文献(3)の(1)式による熱伝達係数を用いた計算値は駒崎らの実測値と良く一致している.熱伝達係数が一定値(1.2及び1.4cal/cm2.s.℃)の場合の解析結果を破線で示した.ゲート速度が20m/s付近で小さい場合にはh=1.2の場合が比較的良く一致し,ゲート速度が60m/s付近で大きい場合にはh=1.4の場合が比較的良く一致している.広い範囲のゲート速度で実測値と良く一致させるためには(1)式で示すような,流速とエアギャップを考慮した場所と時間に依存する熱伝達係数を用いることが重要である.
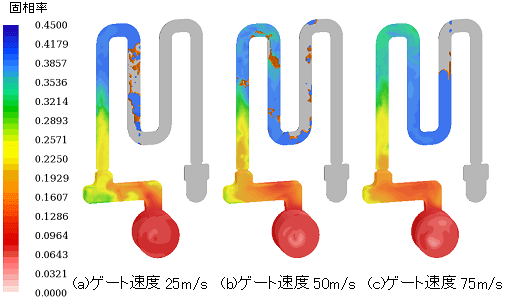 |
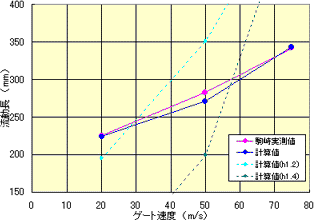 |
図4 薄肉弓字状テストピースの流動停止に及ぼすゲート速度の影響 |
図5 流動長とゲート速度の関係 |
Page TOP
4.ガス巻き込みシミュレーション
ダイカスト製品は湯流れ時に溶湯の乱れによってガスの巻き込み欠陥を発生しやすく,熱処理した際にブリスター欠陥が発生しやすいことは良く知られている.このガス巻き込み欠陥について,図6の模式図で示すようなモデル化をして解析を可能にした.まず,自由表面をVOF法(Volume of Fluid法)で解くことによって左図のようなボイドの発生を予測する.この場合ボイドとは数個以上のメッシュ要素の集合として表されるマクロ的な空洞である.さらに溶湯が充てんされることによってボイドが1要素以下のサイズになって消滅する.このマクロ的な空洞がなくなった時点で1要素以下のサイズの空気巻き込みが発生したとして,空気巻き込み欠陥のサイズ,ガス圧,個数を計算する.
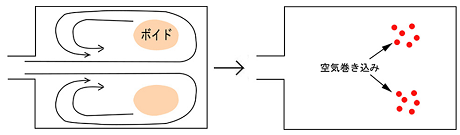 |
図6 ガス巻き込みメカニズム |
2005年12月にNADCA(北米ダイカスト協会)主催で鋳造シミュレーションのコンクールが行われた.対象製品は油圧ポンプ用のエンジンブロックであり,5社がコンクールに参加した.ここでは,CAPCASTの解析例を紹介する.
湯流れ時のキャビティ内のガス圧力を図7に示す.銀地の領域は溶湯が充填されている箇所である.(a)の堰前で高速切替した場合では堰近くの製品部にまだ未充填の箇所がある.また(a)のほうが(b)の製品内で高速切替した場合よりガス圧力は高くなっている.従って,鋳物のガス巻き込み欠陥を減少させるには,(b)の製品内で高速切替した場合のほうがキャビティ内のガス圧が減少して,有利であると考えられる.
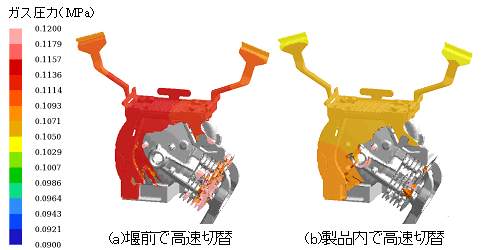 |
図7 湯流れ時のキャビティ内ガス圧力 |
Page TOP
湯流れ完了時の巻き込みガス量を図8に示す.ガス量は大気圧0℃規準での100g当りの量(cc)で表してある.このシミュレーション結果でも(a)の堰前で高速切替した場合のほうが巻き込みガス量が大きくなることが分かる.
湯流れ完了時の巻き込みガス圧力を図9に示す.(a)の堰前で高速切替した場合のほうが,鋳物内の巻き込みガスのガス圧力が高い部分が多くあることが分かる.つまり,(a)の場合のほうが,熱処理時や溶接時にブリスターが多く発生することを予測できるようになってきている.
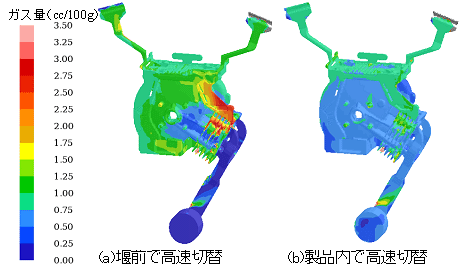 |
図8 湯流れ完了時の巻き込みガス量 |
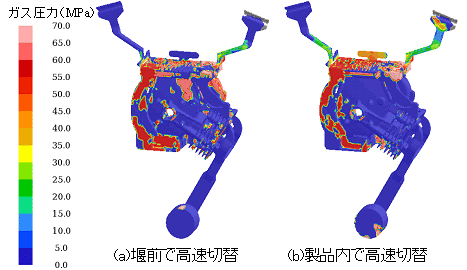 |
図9 湯流れ完了時の巻き込みガス圧力 |
Page TOP
表2に湯流れ完了時の巻き込みガス量の比較を整理した.鋳物部分の体積は1333cm3であり,全巻き込みガス量と平均巻き込みガス量で表示した.堰前で高速切替した場合に比べて製品内で高速切替した方が巻き込みガス量は約40%減少することが分かった.また,スリーブ内でのガス巻き込みを考慮した解析結果は考慮しない場合に比べて約30%巻き込みガス量が増加している.
表2 湯流れ完了時の巻き込みガス量比較 |
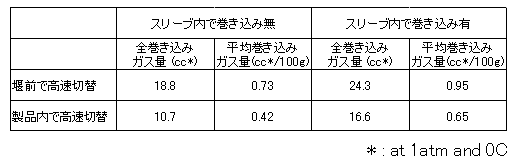 |
Page TOP
5.凝固時のポロシティ欠陥予測シミュレーション
ダイカスト鋳造における凝固時のポロシティ成長の模式図を図10に示す.まず(a)に示すように,湯流れ時に発生した巻き込みガスポロシティが鋳物中に存在している.ビスケット部が増圧されていることによってポロシティサイズは図11に示した値よりも小さくなっている.次に(b)に示すように,鋳物の凝固が進行するとともにビスケット部からの加圧力の効果が小さくなり,鋳物内の溶湯圧力が減少することによってポロシティサイズが拡大される.凝固末期には(c)に示すように,ポロシティ自身が周囲の残留液相の凝固収縮を補給するために,ポロシティサイズが大きくなる.
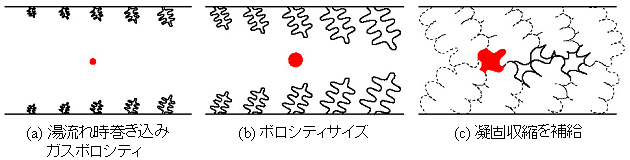 |
図10 凝固時のポロシティ成長 |
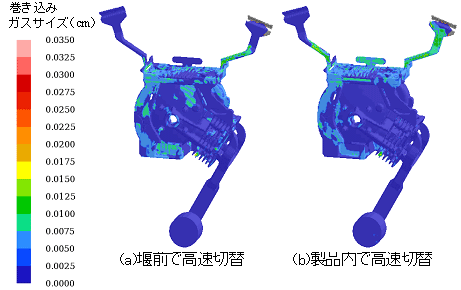 |
図11 湯流れ完了時の巻き込みガスサイズ |
Page TOP
図12に,湯流れ完了後,ビスケット部分から増圧した時点の溶湯圧力分布を示す.(a)は700atm増圧の場合で(b)は200atm増圧の場合である.当然であるが,700atm増圧では鋳物内の溶湯圧力は200atm増圧に比べて相当に高くなる.
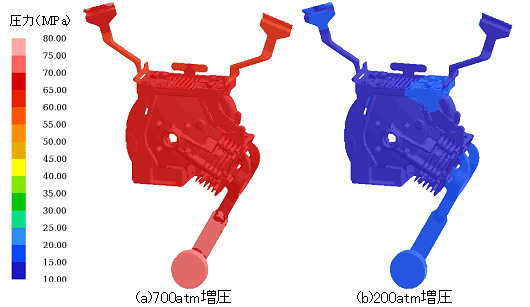 |
図12 増圧後の溶湯圧力分布 |
Page TOP
凝固後のポロシティ量の比較を図13に示す.ポロシティ量0.5%以上の領域を赤色で表示している.ここでのポロシティ量は,図10で説明したように,湯流れ時の巻き込みガスポロシティサイズが増圧でいったん小さくなり,凝固の進行とともに増圧効果が小さくなるためにポロシティサイズが大きくなる.それとともに凝固末期までに周囲の残留溶湯の凝固収縮を補うたためにポロシティがさらに成長したものである.(a)の700atm増圧した場合の方が(b)の200atm増圧に比べて,ポロシティ量0.5%以上の領域はかなり少なくなっている.
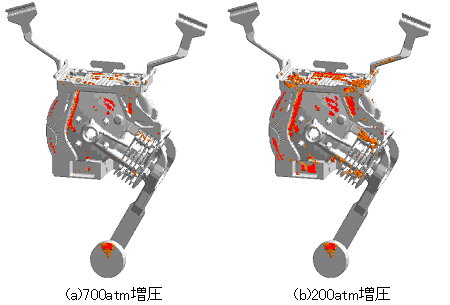 |
図13 凝固後のポロシティ量(ポロシティ量0.5%以上の領域) |
Page TOP
堰前で高速切替した場合の凝固後のポロシティサイズを図14に示す.(a)の700atm増圧した場合では(b)の200atmに比べてポロシティサイズが小さいことが分かる.ビスケット部分からの増圧が大きいとポロシティの成長が抑えられるためである.
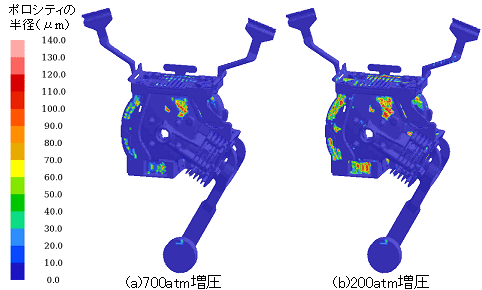 |
図14 凝固後のポロシティサイズ(堰前で高速切替) |
Page TOP
700atm増圧の場合の凝固後のポロシティ量に及ぼす高速切替タイミングの影響を図15に示す.ポロシティ量0.5%以上の領域を赤色で表示している.(a)の堰前で高速切替した場合よりも(b)の製品内で高速切替したほうがポロシティ量が少ないことが分かる.これは,図8に示すように湯流れ完了時の巻き込みガス量が製品内で高速切替したほうが少ないためである.
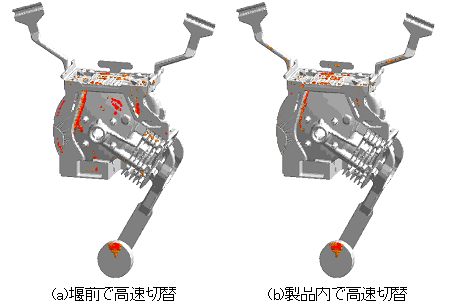 |
図15 700atm増圧した場合の凝固後のポロシティ量に及ぼす 高速切替タイミングの影響(ポロシティ量0.5%以上の領域) |
Page TOP
凝固完了後のポロシティ量の比較を表3に整理した.鋳物の体積が1333cm3に対して,全ポロシティ量(cm3)と平均ポロシティ量(%)で整理した.堰前で高速切替した場合に比べて製品内で高速切替した場合には全ポロシティ量,平均ポロシティ量ともにほぼ半分に減少している.また,増圧が700atmの場合は200atmの場合に比べて全ポロシティ量,平均ポロシティ量ともに約1/3に減少している.
表3 凝固完了後のポロシティ量の比較 |
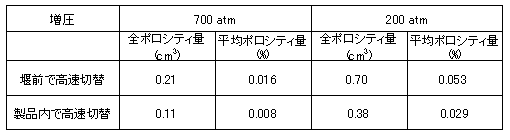 |
Page TOP
従って,ここで紹介した解析例では,製品内で高速切替した場合には,ゲート近くのフィン部分で湯じわ,湯境が発生し易いが,凝固後のポロシティ量は確実に減少されることが分かった.
6.変形シミュレーション
最近,鋳物の凝固,冷却時の割れや変形のシミュレーションが注目されるようになってきた.加工代の減少や鋳肌の加工無し化にも適用されつつある.直交分割の構造メッシュは表面が凸凹であるために,応力の高くなる表面部が異常な応力分布になってしまう.変形シミュレーションには,実物に近いなめらかな表面をもった有限要素法用の非構造メッシュが適している.構造メッシュによって凝固シミュレーションした場合に,変形解析を実施するためには,変形シミュレーション用の非構造メッシュを別に作成し,温度データをマッピングして受け渡しするのが一般的である.凝固及び変形シミュレーションモデルのメッシュサイズが大きく異なる場合には精度良くマッピングすることが困難なことが多い.同一モデルを使用して,湯流れシミュレーション,凝固シミュレーション,変形シミュレーションを連続的に行うことが,迅速で精度の高いシミュレーション結果を得るには重要である.
ダイカスト鋳物の凝固時の寸法変化の一例を図16に示す.鋳物表面と鋳型壁の間にエアギャップが発生していることがわかる.エアギャップの拡大の模式図を図17に表示するが,これにより次式によって鋳物―鋳型間の熱伝達率が求まる.

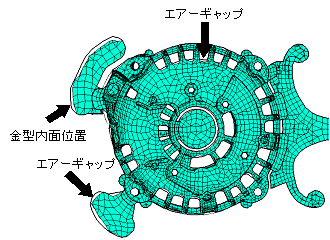 |
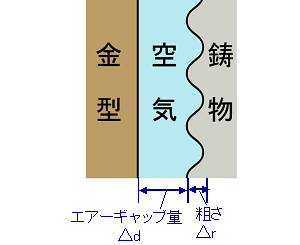 |
図16 金型内での凝固時の寸法変化 |
図17 エアギャップ量から熱伝達率の計算方法 |
Page TOP
湯流れ,凝固シミュレーションにおいて,鋳物―鋳型間の熱伝達率は重要な伝熱定数であるにもかかわらず,適当に決めた一定値を使用することがほとんどであった.上式によって求めた熱伝達率は鋳物の場所によって,また時間によって変化した値が求まる.このような場所と時間の依存性を考慮した熱伝達率を使用することで予測精度が向上すると考えられる.
鋳物変形量に及ぼす鋳型デザインの影響をダイカストケーシング鋳物について調べた.その概略を図18に示す.鋳物形状を(a)に示すが,底面に肉厚のボス部が付いている.材質はADC12,鋳物重量543g,最小肉厚2mmである.(b)が鋳型温度制御の初期デザインであり,冷却パイプと加熱パイプの配置を改良したものを(c)に示す.
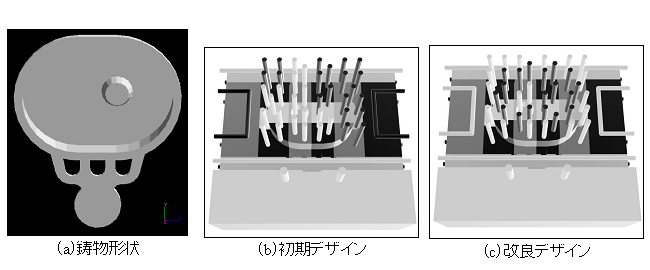 |
図18 鋳物変形量に及ぼす鋳型デザインの影響 |
外部フランジ表面の変形量に及ぼす鋳型デザインの影響を図19に示す.図中の測定基準A,B,Cが一平面になるように座標を変換して垂直方向(Z方向)の変位量を上図に示してある.初期デザインに比べて改良デザインでは相当に変形量が小さくなっているのが分かる.改良デザインでの型開き時の鋳物温度分布に及ぼす熱伝達率の影響を図20に示す.(a)が熱伝達率の場所及び時間依存性を考慮した場合で,(b)が熱伝達率一定の場合である.熱伝達率一定ではフランジ部の温度低下が熱伝達率の場所及び時間依存性を考慮した場合に比べて大きい.実際にはフランジ部は早く凝固してエアギャップが形成され熱伝達率が小さくなるために温度低下が小さくなるはずである.このことによって熱伝達率一定の場合には,製品内での温度勾配が実際より大きくなり室温での変形量が大きくなってしまう.熱伝達率の場所及び時間依存性を考慮した図20の(a)のほうが温度解析精度が良いと考えられる.
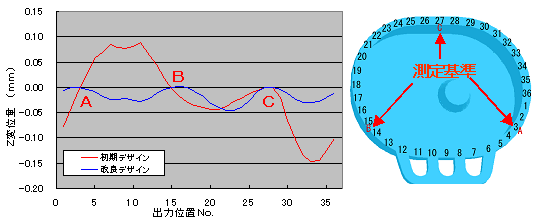 |
図19 外部フランジ表面の変形量に及ぼす鋳型デザインの影響 |
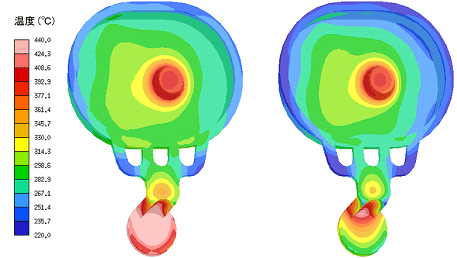 |
図20 改良デザインでの型開き時の鋳物温度分布に及ぼす熱伝達率の影響 |
Page TOP
外部フランジ部表面の変形量に及ぼす熱伝達率の影響について図21に示す.熱伝達率の場所及び時間依存性を考慮した場合は変位量は約10μm程度小さくなる.このように正確な熱伝達率を用いることによって,変形解析の予測精度も向上すると考えられる.
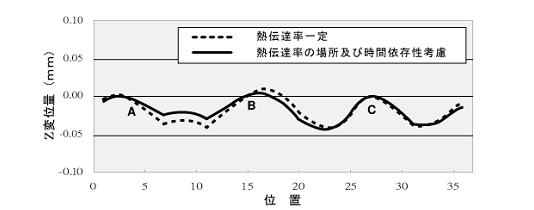 |
図21 外部フランジ表面の変形量に及ぼす熱伝達率の影響 |
Page TOP
7.結言
鋳造シミュレーションを活用することは,試作回数を減少させ,不良率を低下させ,納期を短縮させることが可能になり,地球環境問題の解決につながる.そのためには予測精度が非常に良いことが必須である.形状モデルが正確なことは言うまでもなく,正確な鋳造条件と,物性値を使用することも重要である.もし,シミュレーションの結果が実際と合わない場合には,これらのことが正しく実施されているかを調べることがまず必要である.それでも合わない場合にはシミュレーションの物理モデルを改良する必要があることもしばしばある.鋳造シミュレーションの精度をあらゆる角度から向上させることを目指していきたい.
参考文献
1) 久保:鋳造工学,73(2001)634
2) 久保:鋳造工学,76(2004)1022
3) 久保:鋳造工学,78(2006)620
4) 久保:素形材,49(2008)No.5,6
5) http://qualica.co.jp,JSCASTカタログ2004i
6) 澤田,安斎:鋳造工学,78(2006)629
7) 中道,大塚,前田:日本鋳造工学会第151回講演概要集,(2007)76
8) 駒崎,浅田,渡辺,佐々木,西:鋳物,67(1995)689
9) 蓮野,浅田,村島,岩国,西:鋳物,71(1999)449
(C) CAPCAST INC. ALL RIGHTS RESERVED.
|