鋳造シミュレーションシステムCAPCAST®の開発と最新動向
久保公雄
素形材 3月号に掲載予定
1.鋳造シミュレーションの始まり
1950年代以前の鋳物の引け巣欠陥についての実験及び解析手法は,R.D.Ruddle1)によって1957年に“Solidification of Castings”でまとめられています.
この頃までには鋳物及び鋳型内の温度測定技術が確立されて,かゆ状凝固と表皮形成型凝固の2つのタイプの凝固パターンがあること,
ホットスポット(閉ループ)になる箇所や温度勾配がなくなる箇所に引け巣欠陥が発生することが実験的に明らかにされました.
凝固解析についても,厳密解による解法と数値シミュレーションの両方とも主要な理論は出来上がってきていました.
国内においては,新山先生が1968年に凝固解析の数値シミュレーション方法について日立評論に発表された2)ことをきっかけに,
大阪大学でも大中先生,山内先生の研究室で凝固解析の研究が開始されました.私も,この研究室で1972年に卒論として凝固シミュレーションの研究を行いました.
その後,国内外の大学で大型コンピュータを用いた凝固シミュレーションの研究が広く行われるようになりました.
1980年代には新山先生が日立製作所からパソコンで計算できるプログラムとしてHICASS(鋳物凝固シミュレーションソフト)を出され,
多くの鋳物工場で利用されるようになりました.後に国内外で鋳造シミュレーションのソフトウェア会社を立ち上げた開発者も多く勉強に来られたと聞いています.
新山先生は温度勾配Gと冷却速度RからG/√Rのパラメータで引け巣欠陥を予測することを提案され3),このパラメータはNIIYAMAクライテリオンとして現在でも世界中で使用されています.
2.CAPCASTの開発
米国では1980年頃からNSF(アメリカ国立科学財団)の支援により,
ミシガン大学のPehlke教授を中心として鋳造シミュレーションのプロジェクトを官民一体となって始めていました.
私は1984年からミシガン大学特別研究員としてこのプロジェクトに加わり,新しいポロシティ欠陥予測理論を発表しました4).
その後,日立金属(株)に入社し,素材研究所で12年間鋳物の製造プロセス開発とCAEの仕事に携わりました.
プロセスの開発では湯流れと凝固を制御するために鋳造シミュレーション技術を大いに活用しました.
1998年に日立金属を退社して(有)イーケーケージャパンを設立しました.
CAPCAST®は,弊社が開発し2001年に商標登録した鋳造専用のシミュレーションソフトウェアであり,
CAPFLOW®,CAPPORO®等のモジュールソフトで構成されています.
ソフトウェアの全てを自社開発とすることで,ユーザー様のニーズに迅速かつ的確にお答えできる技術サポート体制を実現しています.
Page TOP
3.有限要素法メッシュ
現在市販されている鋳造シミュレーションシステムのほとんどは直交差分法をベースにしたものですが,
CAPCASTでは形状精度の良い有限要素法メッシュを使用しています.図1に,有限要素法メッシュ,直交メッシュ,混合メッシュの比較を示します.
混合メッシュは直交メッシュを改良したものですが,有限要素法メッシュに比べると形状精度はかなり劣ります.
有限要素法メッシュの要素数は直交メッシュの約1/5,混合メッシュの約1/7と少なく,計算速度の点からも有利です.
特に複雑大物形状鋳物の場合にはメッシュによる要素数の差が顕著になります.
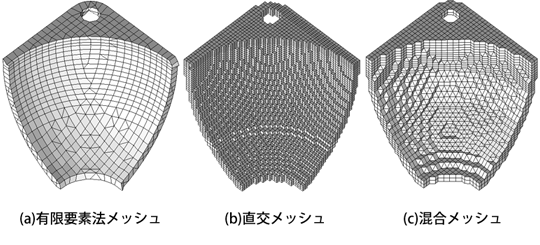 |
図1 メッシュの種類 |
Page TOP
図2に分岐した湯道の湯流れに及ぼすメッシュの影響について示します.分岐した後に一方はy軸に平行な方向に流れ,他方は斜め方向に進むモデルです.
有限要素法メッシュではどちらの方向も同じ流量であるのに対し,直交メッシュではy軸に平行な湯道の流量が大きくなります.
これはメッシュの形状がy軸に平行な湯道では滑らかなのに対し,斜め方向のメッシュは段がついているためです.
有限要素法メッシュは直交メッシュよりも湯流れ解析の精度が良いことが分かります.
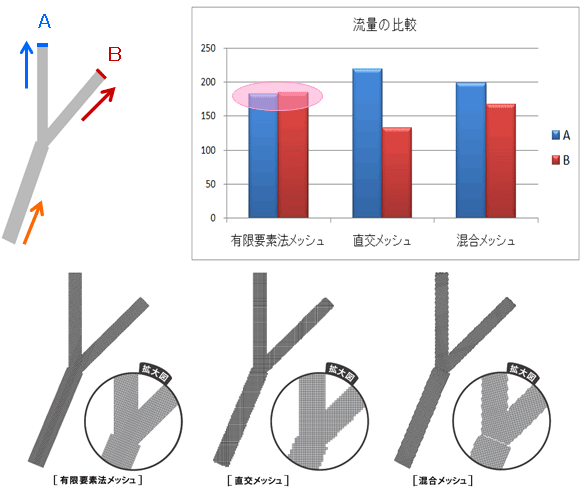 |
図2 分岐した湯道の湯流れに及ぼすメッシュの影響 |
Page TOP
図3にCAPCASTの不連続メッシュを示します.冷却パイプのように細かいメッシュが必要な箇所がある場合,
それぞれのパーツごとに異なるサイズでメッシュ切りができるようになっています.これによりダイカストの冷却パイプは細かいメッシュで,
鋳物や金型は比較的粗いメッシュで切ることができ,全体の要素数を減少させて高速に解析することができるようになっています.
このようなことが可能なのも有限要素法メッシュを使用することでパーツ間の界面形状が正確にメッシュ切りできるためです.
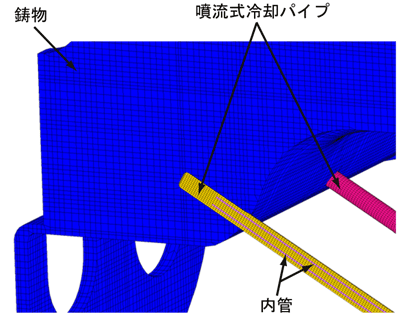 |
図3 不連続メッシュ |
4.湯流れシミュレーション
ダイカストの湯流れ時の巻き込みガス量を図4に示します.低速から高速への切り替えを堰前で行うより,
製品内で行った方が巻き込みガス量が減少することが解析から分かります.また図5,6に示すように,増圧力が大きい程ポロシティ量は少なく,
ポロシティサイズも小さくなることも解析で求まります.これはビスケット部分からの増圧が大きいとポロシティの成長が抑えられるためですが,
このように湯流れ時に巻き込まれたガスが凝固時にポロシティとして成長していく過程やビスケットからの増圧でポロシティ成長が抑えられることが計算できます.
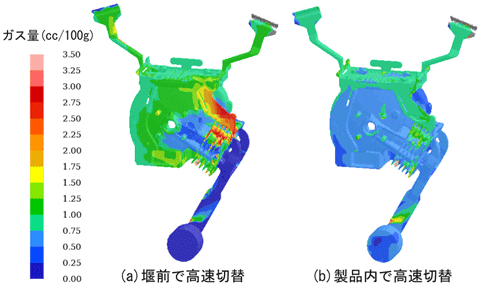 |
図4 ダイカスト湯流れ時の巻き込みガス量 |
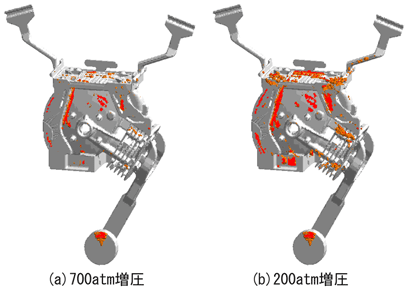 |
図5 堰前で高速切り替え時の凝固後のポロシティ量(ポロシティ量0.5%以上の領域) |
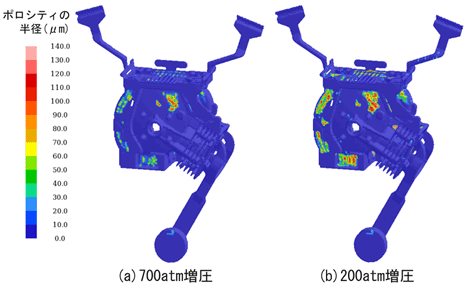 |
図6 堰前で高速切り替え時の凝固後のポロシティサイズ |
Page TOP
湯流れシミュレーションでの機能の一例としては以下のようなものがあります.
|
@ |
ガス相内の圧力勾配を考慮した2相流解析 |
|
A |
不廻り,湯境の直接予測 |
|
B |
鋳型発生ガスによるガス欠陥予測 |
|
C |
表面張力,粘性係数温度依存性考慮 |
|
D |
流速依存(表面法線方向を含む)を考慮した溶湯/鋳型間の熱伝達係数 |
|
E |
ダイカストの高精度プランジャー移動計算 |
|
F |
ダイカスト充填パターンの最適化 |
|
G |
冷却管水流れと金型の連成解析 |
|
H |
スプレイ冷却解析(ノズル位置の時間移動を含む) |
|
I |
低圧鋳造のストークから製品までの全体解析 |
|
J |
遠心鋳造法(注湯口移動の考慮) |
|
K |
半溶融凝固鋳造法 |
|
L |
消失模型鋳造法 |
|
M |
傾転鋳造法(湯溜り設置,多軸回転) |
|
N |
重力鋳造注湯時の湯口カップ上部空隙保持 |
5.凝固・欠陥予測シミュレーション
最近ではX線CTにより鋳物欠陥を検査できるようになり,鋳造シミュレーションの精度向上に大いに役立っています.
しかし,ほとんどの鋳造シミュレーションソフトでは伝熱解析のみによりポロシティ欠陥を予測しており,精度が低いのが現状です.
これは伝熱解析のみで得られた閉ループの情報からホットスポット,NIIYAMAパラメータ等によりポロシティ欠陥を予測する方法です.
閉ループの体積等から簡易にポロシティ量を計算することも行われており,推定ポロシティ量として出力することもあります.
CAPCASTでもこのような予測は可能になっていますが,十分な精度は得られません.
閉ループ法では限界固相率を決め,限界固相率以下の未凝固領域が孤立した場合に閉ループ(ホットスポット)が発生したとします.
一般に閉ループ法では限界固相率は0.3や0.7が使用されますが,
実際にはそれ以上に固まった領域に囲まれても圧力勾配があれば溶湯補給がされるので引け巣欠陥が発生するということにはなりません.
CAPCASTの凝固・欠陥解析では以下の4つの式を連立することでデンドライト凝固を考慮に入れた溶湯補給を解いています.
|
@ |
熱移動方程式 |
|
|
熱伝導基礎式から凝固過程を計算 |
|
A |
運動方程式 |
|
|
凝固中の溶湯圧分布からデンドライト間溶湯補給を計算 |
|
B |
ガス量保存式 |
|
|
固相内,液相内,ポロシティ内のガス量保存の計算 |
|
C |
連続の式 |
|
|
凝固収縮量がデンドライト間溶湯補給量とポロシティ成長量に保存される計算 |
@の熱移動方程式のみによる解析では,肉厚部は凝固が遅れて欠陥が発生しやすいという大まかな予測はできますが,
欠陥ガスの影響や欠陥サイズを計算できません.CAPCASTでは,@に加えてA〜C式も連成して解くことによりポロシティ欠陥を精度良く予測できます.
図7に足回り部品のポロシティ欠陥予測を示します.ホットスポット(閉ループ)が発生しない場所でもポロシティが1%以上発生することが予測できています.
これはCAPCASTを創立した1998年頃にUSCARプロジェクト(米国車メーカー3社の共同研究開発)に参加した際の解析結果です5)6).
鋳鉄部品のAl化による軽量化検討で鋳造シミュレーションが役だった例として報告されています.
この頃から,@〜C式を連立したポロシティの直接予測シミュレーションが注目され始めました.
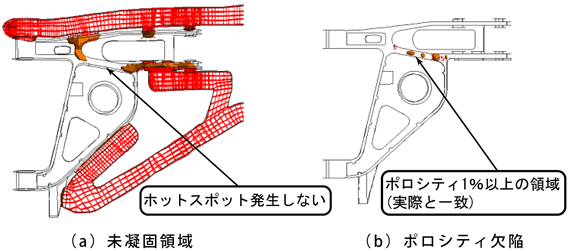 |
図7 溶湯補給係数と鉄量の関係 |
Page TOP
ポロシティ欠陥の予測を精度良く行うためには,シミュレーションに使用する物性値や境界条件の正確さが要求されます7).
例えば,図8に示すようなAC2B合金板状鋳物のポロシティ欠陥に及ぼす押湯幅の影響を調べました8).押湯幅が大きくなれば製品部にはポロシティが発生しなくなります.
図8はFe量が0.5%の場合ですが,Fe量とMn量の組み合わせが少し変化すればポロシティ欠陥が製品部に発生しなくなるのに必要な押湯幅が異なってきます.
これをシミュレーションで正確に予測することは可能ですが,正確な物性値を使用する必要があります.
合金成分が少し違うだけで,図9に示すような温度と固相率の正確な関係を使用する必要があります.
これにより,各合金成分の鋳物の冷却曲線の実験結果と計算結果が一致するようになります(図10).
また,これだけでは十分でなく,図11に示すようなデンドライト間流動のし難さを示す溶湯補給係数としてFe量とMn量により変化する値を使用する必要があります.
これは合金成分によって凝固中のデンドライト組織が変化するためですが,詳しくは参考文献(8)をご参照下さい.
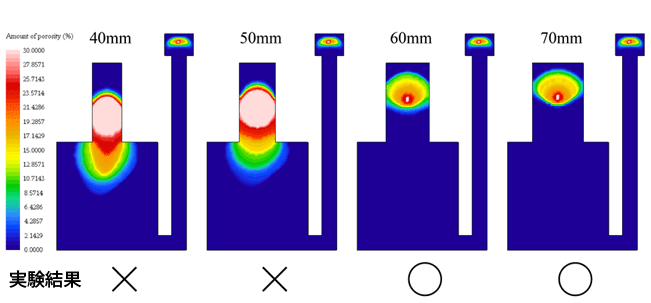 |
図8 AC2B合金板状鋳物のポロシティ欠陥に及ぼす押湯幅の影響(Fe量0.5%) |
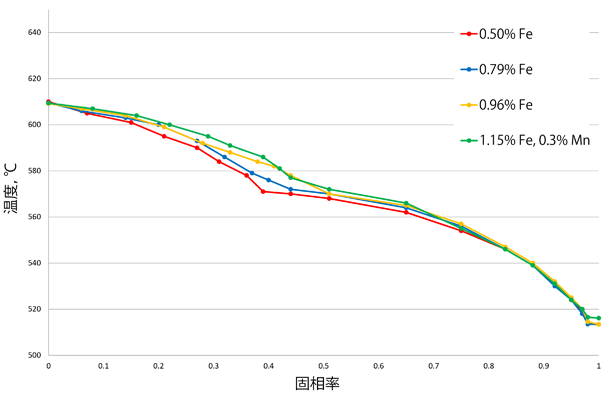 |
図9 AC2B合金の凝固時の温度と固相率の関係 |
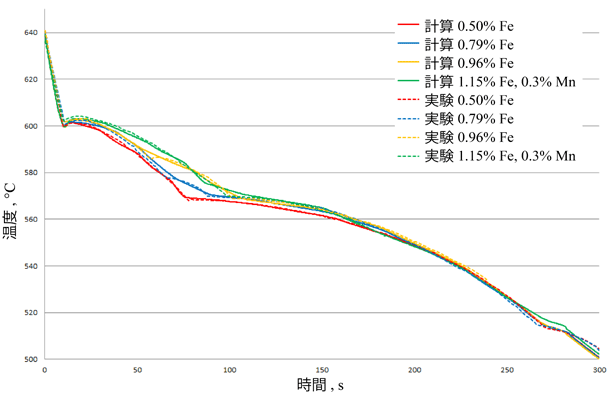 |
図10 冷却曲線の実験結果と計算結果の比較 |
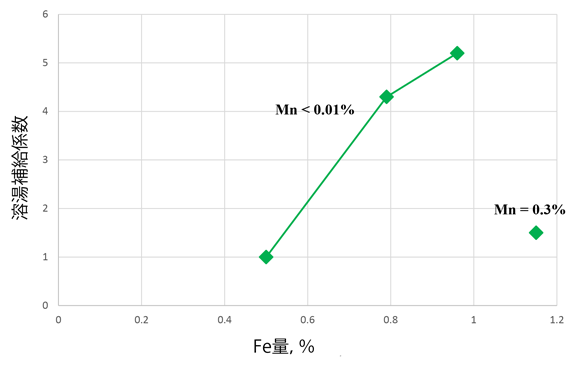 |
図11 溶湯補給係数と鉄とマンガン量の関係 |
Page TOP
凝固・欠陥予測シミュレーションでの機能の一例としては以下のようなものがあります.
|
@ |
球状黒鉛鋳鉄の黒鉛膨張考慮(冷却速度依存性を含む) |
|
A |
球状黒鉛鋳鉄の鋳型壁移動考慮 |
|
B |
A1変態考慮 |
|
C |
過冷凝固 |
|
D |
表面引け欠陥予測 |
|
E |
湯流れ−凝固の連続欠陥解析 |
|
F |
ダイカスト局部加圧解析 |
|
G |
エアーギャップ考慮の凝固解析 |
|
H |
実体強度予測 |
|
I |
金型温度制御のためのサイクル計算のスケジュールタイムの自動調節 |
6.変形シミュレーション
変形シミュレーションには,実物に近く滑らかな表面をもった有限要素法メッシュが適しています.
直交メッシュを用いた凝固シミュレーションの後に変形解析を実施するためには,変形解析用の有限要素法メッシュを別に作成し,
温度データをマッピングして受け渡しするというのが一般的です.このとき凝固と変形のモデルが大きく異なる場合には精度良くマッピングすることは難しいです.
同一のメッシュモデルを使用して,湯流れシミュレーション,凝固シミュレーション,変形シミュレーションを連続的に行うことで,
迅速に精度の高い変形シミュレーション結果を得ることができます.特に,鋳物の割れや金型寿命のように局部的な応力変化が重要な場合に予測精度を向上させるためには,
湯流れ,凝固,変形解析は同一のメッシュで計算することが重要です.要素ごとの局部応力が割れの判断になるため,要素ごとの正確な温度,固相率,
ミクロ偏析を正確に使用することが予測精度を向上させるためには必須です.
ダイカスト鋳物の凝固時の寸法変化によるエアーギャップの一例を図12に示します.鋳物表面と鋳型壁の間にエアーギャップが発生していることがわかります.
エアーギャップ量を予測することにより鋳物/鋳型間の熱伝達率を求めることができます9).
ポロシティ量のシミュレーション結果がX線CTの実験結果とどうしても一致しない場合には,
鋳物/鋳型界面のエアーギャップ量から求めた熱伝達率を使用してシミュレーションを行うことが多くあります.
熱伝達率を一定値や温度依存性の値として使用するよりも,場所と時間によって変化するエアーギャップから求めた熱伝達率を使用することが,
欠陥予測の精度を向上させるために重要です.エアーギャップの計算は有限要素法メッシュを一貫して使用していることによって可能な技術です.
 |
図12 エアーギャップ |
Page TOP
図13にキャビティ形状設計の一例を示します.解析で求めた変形量を基にキャビティ形状を補正することで,
変形後の最終的な寸法精度を向上させることが出来ます.この計算方法は次の通りです.まず解析結果の室温における寸法と目標の製品寸法の差を求めます.
寸法差が許容範囲内に収まらない場合,予測した変位量を基に高温での製品形状を補正した解析モデルを出力し,鋳造変形を再計算します.
これを寸法許容誤差の範囲内になるまで繰り返します.このような鋳造シミュレーションソフトの変形量予測に基づくキャビティ形状設計方法は今後有効になってくると考えます.
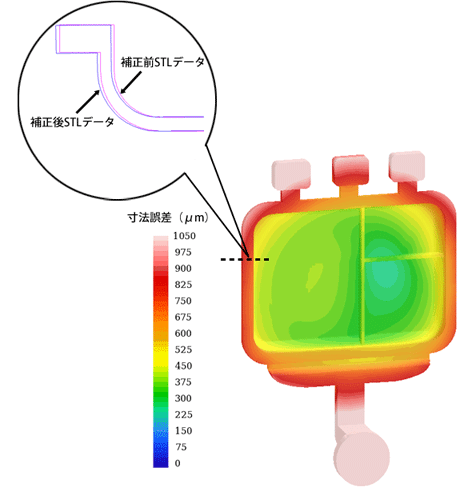 |
図13 キャビティ形状設計 |
Page TOP
変形予測シミュレーションでの機能の一例としては以下のようなものがあります.
|
@ |
湯道切断によりモデル形状が変化した解析 |
|
A |
変形後の形状で目標製品寸法との差を計算 |
|
B |
冷却過程の鋳物,鋳型の割れ発生温度を要素ごとに表示 |
|
C |
鋳物の割れでミクロ,マクロ偏析による凝固遅れとミクロポロシティの影響を考慮 |
|
D |
金型寿命予測 |
7.マルチスケールシミュレーション
マルチスケール鋳造シミュレーションの概略を図14に示します.大きくマクロスケール,メゾスケール,ミクロスケールに分けられます10).
マクロスケールには,前章までの湯流れ,凝固,欠陥,変形解析が含まれます.
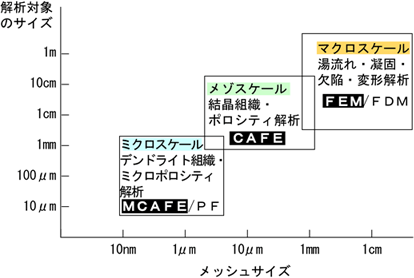 |
図14 マルチスケール鋳造シミュレーションの概略 |
Page TOP
AC4CH合金コニカルモールドについてマクロスケールでの欠陥予測を図15に示します.
鋳物頂部から垂直方向に円柱状の大きな中心線引け(ピンク色で表示)が予測され,鋳物中央部にはミクロポロシティ(緑,青色で表示)が予測されています.
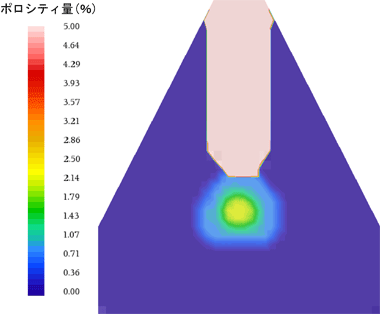 |
図15 マクロスケール欠陥予測 |
Page TOP
図16にAC4CH合金コニカルモールドのメゾスケール結晶粒組織及びポロシティの解析結果を示します.
黒く塗った領域は空洞であり,頂部から中央部に大きなパイプ状の空洞が発生しています.また鋳物中央部にミクロポロシティが点在していることも分かります.
100μm程度のメッシュサイズでポロシティ相か結晶相かの判定が出来るので実験結果と直接的に比較し易い解析結果が得られます.
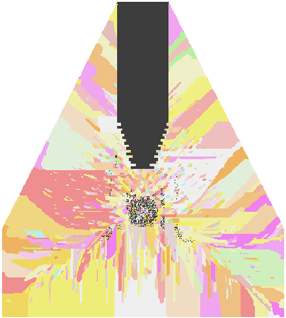 |
図16 メゾスケール結晶粒組織及びポロシティの解析 |
Page TOP
ミクロスケールの解析は,1μm程度のメッシュサイズでデンドライト組織やミクロポロシティを予測する技術です.
一般的にはフェーズフィールド法を用いて解析することが多いですが,CAPCASTではMCAFE法という新しい方法を開発しました10).
フェーズフィールド法は1つのデンドライトのみを詳細に解析することに適しており,核生成の位置を予測することが不得手のため複数のデンドライトを解析することは難しいです.
しかし,鋳物においては核生成を考慮した多数のデンドライトの同時成長を解析できなければいけません.
MCAFE法により多数のデンドライトを同時に解いたAC4CHのミクロ組織の解析結果と実験結果の比較を図17に示します.
デンドライト間にSi相が現れ,全体的に実験結果と比較的良く一致したミクロ組織が得られています.鋳物のミクロスケールシミュレーションを行うことにより,
ミクロポロシティの予測が可能になり,耐圧洩れ性や疲労強度等の多くの鋳物特性の予測に将来活用されるようになると考えられます.
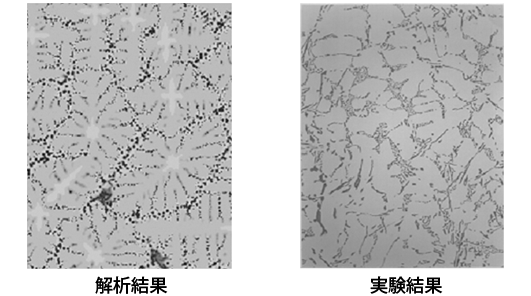 |
図17 ミクロ組織の解析結果と実験結果の比較 |
Page TOP
図18にAC4CH合金コニカルモールドの外引けの解析結果を示します.
外引け欠陥は球状黒鉛鋳鉄等の固液共存域が大きく鋳物表面部の凝固が遅くなる場合に発生し,このモデルでは円錐側面部に外引けが発生することを解析で求めました7).
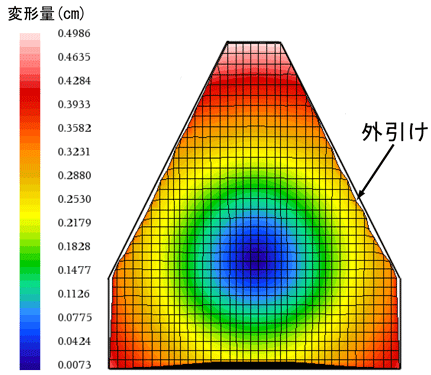 |
図18 外引け欠陥予測結果 |
Page TOP
8.鋳造シミュレーションのこれから
鋳造産業においては,コンピュータシミュレーションを利用することで鋳物の品質向上や納期短縮に役立つようになってきました.
さらに望まれていることは,予測精度を向上させ,シミュレーションだけで最終的な方案と鋳造条件を決められるようになることです.
そのためには,多数の解析を短時間で同時に行えることが必要です.少ない要素数で解析できる有限要素法メッシュを使用することは精度,速度の両面において優れており,
鋳造産業においても今後さらに広く使用されるようになっていくと考えられます.
ポロシティ欠陥の予測においては,熱移動計算のみから閉ループを計算して欠陥を予測する従来の方法では不十分であり,より高精度な解析が求められています.
熱移動計算だけではなく,デンドライト凝固を考慮に入れた溶湯補給を解析することでより直接的に欠陥を予測することがCAPCASTでは可能です.
また,実測結果と合わない場合には,使用されている物性値,境界条件について値を調整して実際と一致させることが重要です.
これは,鋳造プロセス毎に種々の工程があり,合金の成分の微少な違いによる物性値の変動や境界条件の不確かさ等があるからです.
それでも一致しない場合は物理モデルを検討してソルバーを改良する必要があり,全てのソフトウェアを自社開発している弊社では迅速な対応が可能となっています.
参考文献
1) R.D.Ruddle:The Solidification of Castings(The Institute of Metals)(1957)
2) 新山英輔:日立評論,50(1968),5,82
3) 新山英輔,他:鋳物,52(1980)635
4) K.Kubo , R.D.Pehlke : Metall. Trans. 16B (1985),359
5) M.McLaughlin, C.W.Kim, K.Kubo :Trans. AFS, 110(2002),223
6) A.Gohkle :Investigation of mule casting, USCAR QRM #3, Peoria, IL(2000)
7) 久保公雄:鋳造工学,83(2011),399
8) 久保順:鋳造工学,87(2015),759
9) K.Kubo :Proceeding Modeling Casting Solidification Process VI,(2004),281
10) 久保公雄:鋳造工学,83(2011),485
(C) CAPCAST INC. ALL RIGHTS RESERVED.
|